MAINTENANCE PACKAGES
Sykes Group offers a range of preventive maintenance and service options, contact your Sykes Group representative for a tailored service quote for your site.
250 Hour Service
Routine and Preventive Maintenance is crucial for the longevity of your equipment. A maintenance check on a stand-by generator every three months includes the following:
- Check all shut-down alarms for correct operation
- Check all non-critical alarms
- Check oil level
- Check coolant level
- Check coolant inhibitor level
- Check battery condition
- Check operation of jacket water heaters (if applicable)
- Check battery terminals
- Check battery charger operation
- Check all components on control board for correct operation
- Visual inspection of genset and report
- Visual inspection of air filter elements and when necessary, renewal
- Drain any water/sediment from the primary fuel filter
- Check that auto start/time is with specification for mains failure (if applicable)
If we find during a routine service that another area needs attention, we’ll get your approval before we proceed with the work. Any additional work will be charged at the normal field service rate, plus parts.
If any work is scheduled outside of normal trading hours, an overtime rate will be charged.
Air filters will be changed whenever needed, and charged accordingly.
500 Hour Service
A six-month preventive maintenance plan for your stand-by generator covers everything a three-monthly service would cover, plus the following tests and inspections:
- Carry out three-monthly checks
- Sample oil and top up if required
- Check level and condition of coolant
- Test oil pressure shut-down switch
- Test high water temperature and shut-down switch
- Check all cable connections at alternator and panel
- Check for oil, fuel and water leaks
If we find during a routine service that another area needs attention, we’ll get your approval before we proceed with the work. Any additional work will be charged at the normal field service rate, plus parts.
If any work is scheduled outside of normal trading hours, an overtime rate will be charged.
Air filters will be changed whenever needed, and charged accordingly.
1000 Hour Service
The 12-monthly service is our most comprehensive preventive maintenance and service programme. It includes the following checks on operations components:
- Change oil and filter
- Change fuel filter
- Change coolant filter
- Change air filter if required
- Check level and condition of coolant
- Check cable connections at alternator
- Check fuel pump operation
- Check for oil, fuel and water leaks
- Check that the radiator is clean and free from debris
- Check the condition and tension of all drive belts
- Ensure that the mounting nuts for the turbo-charger are tightened securely
- Check all shut down alarms for correct operation
- Check all non-critical alarms
- Check battery condition
- Check operation of jacket water heaters (if applicable)
- Check battery terminals
- Check battery charger operation
- Check all components on the control board for correct operation
- Check restriction indicators for air filters and when necessary, replace
- Check auto start/time is with specification for mains failure
- Visual inspection of gensets and report
If we find during a routine service that another area needs attention, we’ll get your approval before we proceed with the work. Any additional work will be charged at the normal field service rate, plus parts.
If any work is scheduled outside of normal trading hours, an overtime rate will be charged.
Air filters will be changed whenever needed, and charged accordingly.
Extended Service Contracts
For added peace of mind, you can purchase an Extended Service Contract. The Extended Service Contract covers replacement costs and labour for major equipment components, including engines, electronic governing systems, radiator, fuel tank, engine control panel main control boards, alternator main components and bearings, AVR and enclosures.
The Industries we Serve
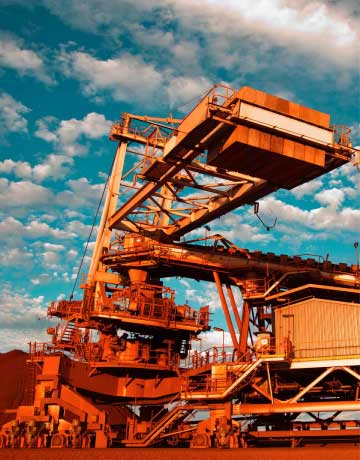
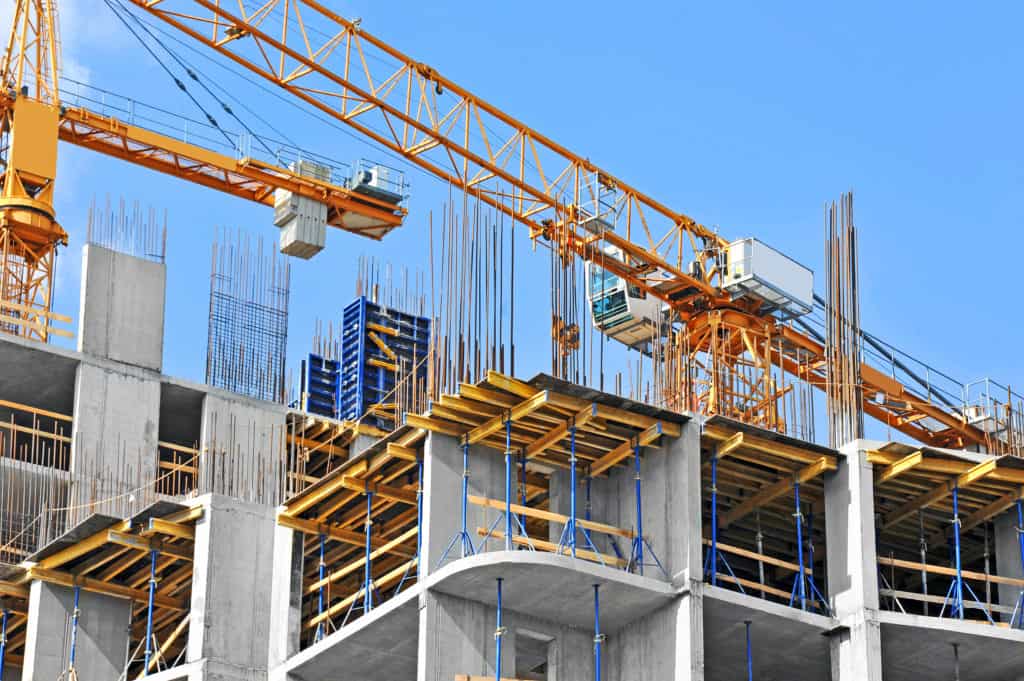
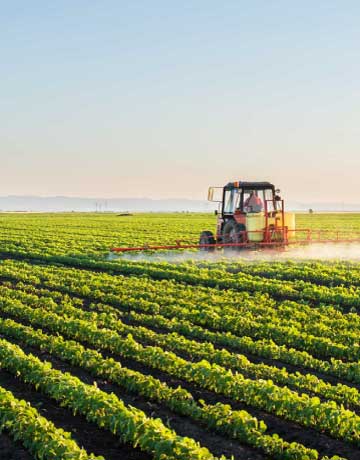
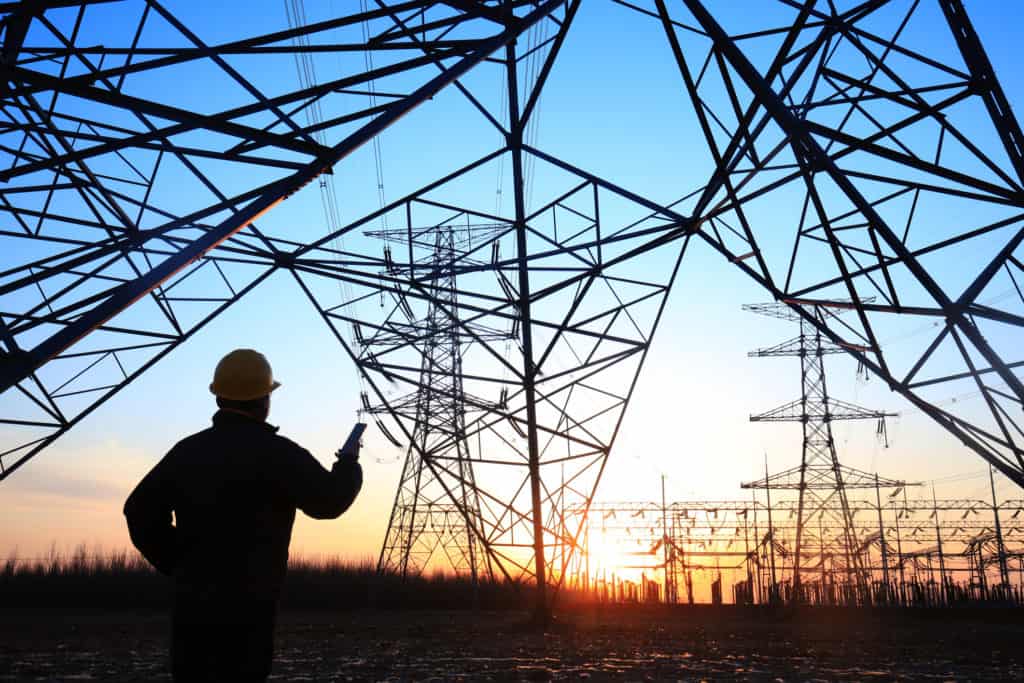
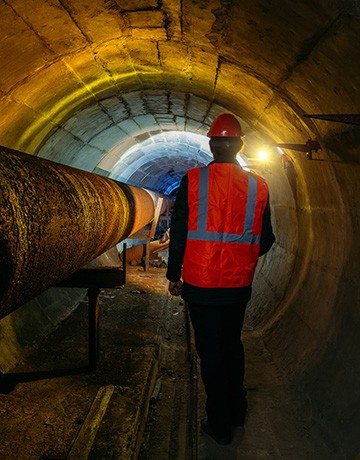
WHY Sykes Group?

DIRECT COMMUNICATION
Our in-house engineers and tech experts will work with you to create bespoke solutions for your project.

PREMIUM SPECIFICATIONS
Our pumps are designed to handle the most challenging and demanding environments. Using our in-house engineering team, we can custom-design pump packages to match any specification.

OPERATION AND MAINTENANCE COSTS
We design and manufacture pump packages that delivers optimal efficiency and minimal downtime. Even operating in harsh conditions, our products provide a safe and cost-effective solution.

EQUIPMENT RANGE
We provide a wide range of pumps to handle all types of water-based issues. Whether above or below ground, Sykes Group can offer a solution.

CUSTOMER SERVICE AND AFTERMARKET
If you need advice on a particular part, our parts and customer service technicians are always available to offer qualified, professional advice.

STOCK AND MANUFACTURING
As the original equipment manufacturer (OEM), we keep plenty of stock on hand and can provide quick access to the parts you need.